Drill pipe handling is a required skill in offshore drilling safety because tubulars are the most common piece of equipment in the upstream section. Due to their heavyweight, large numbers, and round shape, they can easily cause incidents. In fact, according to the International Association of Drilling Contractors (IADC), drill pipes are the cause of most injuries on oil rigs. That is why HSE managers should be aware of all related hazards and be prepared with intelligent HSE solutions.
Table of content
Material handling is estimated to have caused 25% of all recordable incidents on European drilling rigs in 2020. This portion is more than 15% in onshore drilling and 21% in offshore drilling in the middle east.
This article will review 3 common hazards in drill pipe handling and offer effective safety measures to prevent them.
3 Common hazards in drill pipe handling
Work hazards are the biggest concern of all HSE professionals in oil rigs who work hard to mitigate the risks. Drill pipes are among the most concerning equipment that creates the following hazards:
1. Struck by and caught between drill pipes
Drill pipes are a critical part of oil well operations that are unloaded from a truck, loaded to rack, moved on the catwalk and pipe ramp to the drilling floor through the V-door, and placed into a mousehole. Catline might be used for delivery process, but air hoist or hydraulic winch are used as well. Considering the large number of connections that is required for everyday operations, the possibility of a worker being struck by a drill pipe is strong. Being bundled together in offshore work environment just multiplies the risk.
Suspended, hoisted, or moving drill pipes might fall and seriously injure staff. Rolling pipes are also a common scene in oil rigs that cause staff tripping and consequent injuries. Workers can easily get caught between tubular on the rack if only one pipe rolls accidentally.
There is also other equipment such as tongs, kelly, collars, and make-up chains that are spinning and swinging around rotary table and can trap workers between themselves and the pipes.
2. Hand injuries
Hands have the most direct contact with drill pipes, and despite the fact that there are many hand safety tools, hand-related hazards are very common. They contribute to 50% of incidents in the oil and gas industry. Crushes, blunt force impacts, pinched fingers, and even severe abrasions and lacerations to the hand frequently happen, resulting in workdays lost, claims, and costs.
According to National Safety Council, average cost of a single hand injury amounts to $21,918.
Among all crew members, drillers, floor hands, derrick hands, tool pushers, and production operators are more at risk of hand injury compared to others.
Hands-Free safety tools are constantly developed in the industry to protect workers, but human error always plays a role in accidents!
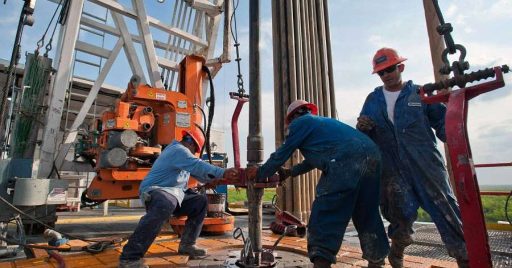
3. Slips, trips, and falls
Fluid splashes on the ground can cause slips and falls. Small objects and equipment that are always around or poor housekeeping might cause trips. Tubulars themselves can roll and trip someone if handled carelessly. The risk of falling becomes greater if working from height is considered.
The injuries range from bruises and wounds to broken bones, all of which permanently impact workers’ life.
4 Effective Safety Measures in drill pipe handling
In order to mitigate the risk of safety hazards in drill pipe handling, tight regulations and standards are set in place by various organizations that can be summarized in the following 4 safety measures:
1. Proper positioning of staff
There are no-go zones and red zones when it comes to standing positions during operation. Lifting procedures are the best example that carries high risks of falling drill pipes. Their movement path from the rack to the catwalk and rig floor should be clear of staff.
Standing on drill pipes is a dangerous behavior that can cause rolling and consequent falls. Standing in tong swing radius or too close to rotary table when it is rotating are also high risk behaviors. Proper distance is also required In breaking out or making up processes.
The worker must not be on top of the pipe that is unsecured, between the pipe and the pipe racks or tubs, nor in an area that is made hazardous by potential pipe movement.
Standing too close to edges when working from height is always a bad idea even if operation is not underway. Momentary loss of footing can lead to severe injuries.
Crew coordination managed by rig supervisor is the key to workplace safety when it comes to drill pipe handling. Knowing task distribution and positioning will reduce incidents.
2. Proper lifting technologies
Tools and machinery are used to provide exceptional control over the load and a safe distance for workers in order to prevent incidents. They complement human ability to move drill pipes across oil rig.
Cranes, elevators, linear lifts, scissor lifts, pipe skate machines, powered baskets and forklifts are common machinery on site that are innovated rapidly to provide better workplace safety. But frequent maintenance is the key to their service to workplace safety otherwise they become a source of hazard!
Beside using machinery, simple safety measures can prevent major incidents. For example, racks should always be properly leveled and pipes should be chocked to prevent inadvertent movements. In V-door, they should be snubbed to prevent sliding down the beaver slide.
A combination of large and small technologies can make drill pipe handling more safe.
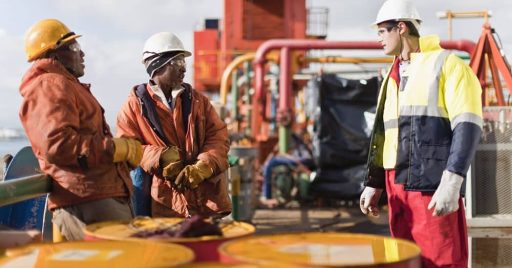
3. Using proper PPE
Sometimes, people who work around the pipe rack, load and unload tubular, or lift pipe through a winch or other machinery on the rig floor are not wearing proper PPE. The inadvertence could cause serious injuries or even death.
Therefore, HSE managers need to find ways to encourage workers to wear essential safety gear, such as helmets, gloves, and shoes. Up to now, adding more safety supervision and improving safety culture have been the best solutions. But now, thanks to the advancements in technology, HSE managers can detect PPE violations using AI-based safety software.
4. Frequent pipe inspections
Periodic inspection and replacement of drill pipes insure their integrity is intact. Harsh conditions of oil rig environment and elemental factors will impact the pipes resulting in corroded surface and deformity both of which can be harsh on workers’ hand.
A spherometer is used to quickly measure the radius of a pipe so it can be classified for appropriate action. N-Class is the new pipe quality while P-Class shows some signs of wear and C-Class is approaching the end of its life and should be graded for scrap.
Following best practices in drill pipe handling extends their life cycle. Using chocks, bumper rings, and lifting bails are necessary at every step of operation to prevent surface to surface contact and corrosion. Thread protectors at both end of each section can reduce elemental impact. Lubricant can reduce surface contact with air resulting in less corrosion.
Well-protected drill pipes will create less hazards on the hands and also last longer.
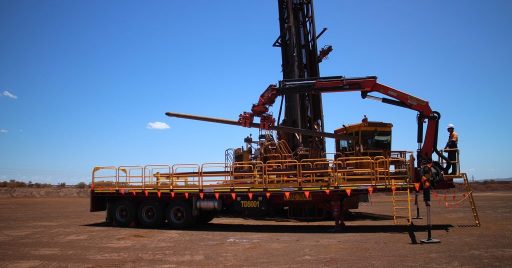
Conclusion
Drill Pipe Handling is the art of oil rig supervision. If performed with effective safety measures, the hazards are minimized and workplace safety remains at its highest.
Being struck by drill pipes, receiving hand injuries, slips, trips and falls are the common hazards in drill pipe handling. They can be effectively managed by well positioning of staff, proper lifting technologies, wearing high-tech gloves and frequent pipe inspections.
But above all, an Intelligent HSE Solution can take drill pipe handling to the next level of safety that results in saving lives and also saving on operation expenses for offshore oil and gas industry.