Safety incidents in oil refineries might cause the loss of many lives and a huge amount of damage to properties. Unfortunately, they are very common! That is why HSE managers should always look for more intelligent HSE solutions to achieve workplace safety goals and prevent common incidents in oil refineries.
According to the U.S. Occupational Safety and Health Administration (OSHA), the fatality rate in oil and gas industry is 7 times higher than in other industries! The U.S. Center for Disease Control and Prevention (CDC) also reported that during 2003–2013, the number of fatalities in this industry increased by 27.6%, reaching a high level of 1189 deaths!
Even the highly regulated safety standards set by organizations such as API are not able to fully prevent these incidents.
In this article, we review 5 common safety incidents in oil refineries. They pose a very real danger to human life, the environment, and assets. Since they are very common, it is a good idea to know what causes them in the first place.
Table of content
What causes safety incidents in oil refineries?
Limitations of detection systems in refineries are often the underlying cause. Despite the fact that current detection systems do a good job of protecting human life, environment, and property, incidents still happen. The reason is that the detectors have limited capability in their technology and they are also limited by the conditions in the refinery structure.
The current detection technology is not able to detect all possible gases that are released into the air. Those gases are often toxic to humans that can silently damage health to a great extent. Some of them are also very explosive!
The structure of refineries is complex, full of columns and tanks that can obstruct the field of sight for detectors, preventing them from identifying real dangers.
There are also confined spaces that might be just a pool of toxic gases, undetectable to human senses. These gases can silently kill the staff. These spaces also limit the portable detectors from extended view so the range of detection is very narrow which makes the range of incidents very wide!
A major setback in current systems is the frequent false alarms raised by detectors. It is partly due to high levels of moisture in the air, but the chemical intensity is also present.
Without frequent testing and calibration, current detectors will not be able to identify actual threats. They need regular cleaning and battery recharge or replacement. Considering the number of devices in each refinery, the cost is too high which prevents the application of maintenance work.
According to the U.S. Occupational Safety and Health Administration (OSHA), the fatality rate in the oil and gas industry is a staggering sevenfold higher than in other industries!
These limitations in current detection systems in oil refineries have a high cost from every possible angle.
There is also the human error factor. The downstream industry is labour intensive and even personal protective equipment (PPE), which are mandatory on sites, are not effective without supervision. Not properly wearing a helmet, mask, vest, harness, goggles, and gloves can expose workers to chemical and mechanical hazards. Unless there is an intelligent monitoring system in real-time that enforces such regulations, incidents will continue to happen.
What are the most common safety incidents in oil refineries?
Now that we know the causes, we can review the 5 most common incidents that happen all around the world:
1. Vehicle accidents
According to OSHA, 4 out of 10 fatalities occur due to vehicles with heavy loads transiting between sites or on highways.
Cranes, forklifts, telehandlers, and crates are the most common bad actors that can strike a worker in their path. Bad weather and road conditions greatly contribute to a high rate of accidents. Speeding is another factor that is common in highways around facilities.
2. Object contact
Tubulars are the main offenders by 12% rate of incidents. Workers might be struck by them or get caught between them.
High-pressure hoses and lines, chains, heavy equipment, and machinery such as overhead cranes are also big players.
Workers might be struck by falling or flying objects, most of which have heavyweight.
The majority of these incidents occur due to ignorance of safety tags and markings.
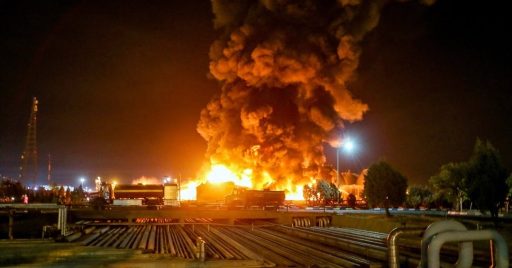
3. Fire & explosion
Oil refineries also have more deaths from fire and explosion than any other industry due to explosive vapors and ignition sources.
There are many hot works performed on the site that incorporate open flames or create welding sparks. Even idling engines and site lighting can easily initiate fire if a flammable chemical is present. Even worse are static electricity and changing weather conditions that don’t have an odor and yet can contribute to the risk.
Real-time monitoring of site conditions such as lighting, temperature, humidity and wind, and ignition sources, and chemical clouds can predict risk and raise the alarm when the conditions are approaching a dangerous level.
A major fire and explosion occurred in 2009 in Petroleum Refinery in Puerto Rico that caused massive damage to 17 petroleum storage tanks while the closing neighborhood also received severe damage. It started with a tank being overflowed when gasoline was being unloaded from a tanker ship to the tank farm. The released vapor cloud caused the explosion. The CSB (U.S. chemical safety board) report identified the source of the incident as a simple failure of the side gauge transmitter in the tank, which stopped the transmission of data to the computer system. Therefore, the operator was not able to observe the trends and identify overfilling of the tank. This incident highlights the importance of regular equipment maintenance and proves the necessity of real-time monitoring by an intelligent system.
A similar fire incident happened in the crude unit of Chevron Refinery in Richmond, California. In 2012, a vapor release from a pipe rupture caused a massive fire and explosion. 18 staff were caught in the vapor cloud, but thankfully, they were able to find the way out before the explosion. However, the particulates and smoke reached surrounding areas and affected 15000 people with chemical exposure symptoms such as breathing problems, chest pain, sore throat, and headache, 20 of which were admitted to hospital. The bad actor, in this case, was the pipe corroded by sulfidation, which is highly aggressive on carbon steel pipes. This case highlights the necessity of routine preventative maintenance inspection that can be automated with intelligent technology.
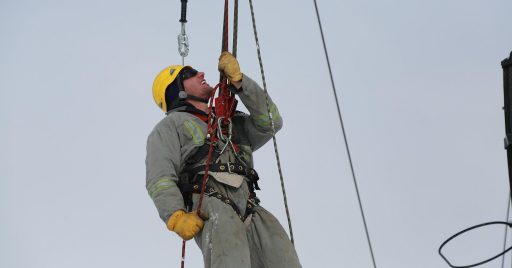
4. chemical contact
Gas & oil leaks are common in refineries some of which are easily identifiable due to their foul odor such as poisonous hydrogen sulfide.
However, some gases are odorless, which makes detection difficult for humans.
The chemical exposure is not limited to the inhalation route, and skin can also come in contact with highly abrasive materials such as Solvents, Pb, and PAHs. Ingestion might also happen, which causes severe digestive upset. Silica, DPM, and VOCs can cause mixed exposure, which multiplies the health damage!
Two unfortunate incidents of chemical exposure happened in the alkylation unit of Tesoro Martinez Refinery in 2014. These alkylation units contain both hazardous acid catalysts and light hydrocarbons. In the first incident, the release of 84,000 pounds of sulfuric acid burned two employees. The second incident resulted in a spray of acid that injured another two workers. The operation was non-routine maintenance work which highlights the importance of pre-identified safety scenarios.
5. Slip & fall
Statistics reveal that just in the U.S., 247,120 non-fatal cases involving falls and slips occur annually. The number is more or less the same in other countries. The majority of incidents happen due to improper use of PPE and bad posture, but poor housekeeping practices are also a big contributor that conceals hazards.
Refinery operations must go on even in extreme weather conditions, no matter winter or summer. Therefore, slips and falls can always happen. Many works performed at height require ladders, stairs, or elevators that set the perfect conditions for falls when the harness is not properly connected to an anchor point or when the worker is standing too close to the edges without supervision.
There are also open pits and floor holes that cause trips. The rolling shape of pipes might also cause slip and fall. Poor lighting at night and talking on a mobile phone are just additional causes for trips that result in strains and cuts.
The wrong posture when pushing and pulling heavy loads, lifting, bending and reaching overhead will lead to trips and ergonomic injuries.
Conclusion
Limited HSE systems cause 5 common safety incidents in oil refineries because they cannot monitor human and machine error in real-time.
The incidents involving vehicles, explosives, object contact, chemical exposure, and slip & fall can be prevented by using a seamless technology solution for effective HSE.
An automated detection technology that identifies all possible threats and pre-defined scenarios in real-time seems like the perfect solution to prevent tragic safety incidents in oil refineries.