Rig floor safety is of the utmost importance due to a large number of workers, huge volume of flammable fuels and expensive infrastructure. Smallest safety incidents can cost many lives and damages to the assets. There is also the risk of environmental damage that has long-term consequences. Only an Intelligent HSE solution can provide maximum rig floor safety and assist HSE managers in their task of protecting staff, property and environment.
That is why we are offering a brief guide to rig floor safety to help HSE managers make intelligent choices.
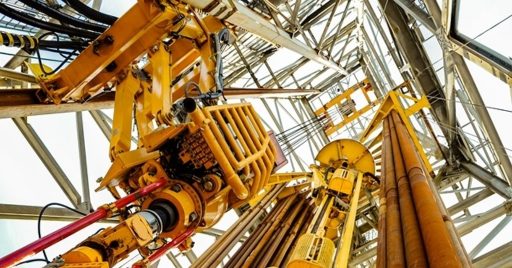
What are the risks in rig floor safety?
Rig floor is the heart of oil and gas industry where the actual product is extracted from the well. It is the site of main upstream operations with several stages, each of which has its own safety hazards and requires specific safety measures to mitigate the risks.
When drilling ahead initiates, there are huge number of drill pipes moved around that can easily strike workers and lead to trips and falls. Hand injuries caused by drill pipe handling are the most common when it comes to drilling rig safety. Other components of drilling operation such as tongs, kelly, rotary table and chains can also cause accidents. There is drilling fluid and many chemicals too that can cause severe reactions and burns.
Then comes the tripping in and out stage when some part of drill string requires changes and replacement. Elevator and stump can pinch and strike fingers and excess drill fluid can splash.
Periodically, the casing operation takes place to line the well hole with massive pipes. Casing, collar and high pressure lines can easily cause injuries.
Regular maintenance is absolutely essential for safety but also puts the staff at risk. Fingers being pinched by machine guards, eyes being harmed by flying metals and skins being burned by hot fluids are commonly reported in maintenance operations.
The well itself should also be controlled for right pressure to prevent blowout. Heavy duty hoses can hit workers and fluid can splash during such operations.
On the other hand, there are onshore and offshore rigs that have their own set of safety challenges. On land, there is extreme temperature in either ends of spectrum. It can be hot and humid or cold and freezing. At sea, there is possibility of storm, wind, humidity and sun exposure.
And above all, there is the danger of fire and explosion always looming over rig floors.
According to CDC data, 71% of fatal injuries occurred in upstream section in 2017, 36% of which were on rig floor. With such a rate of fatality and wide range of risks, rig floor safety is the number one priority in oil rig safety to protect humans, environment and property.
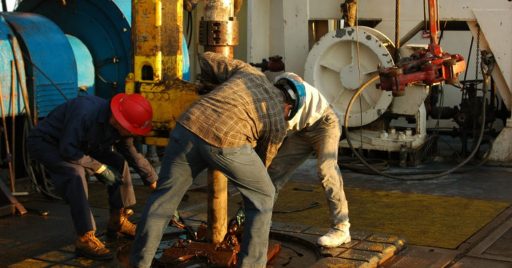
How to maximize rig floor safety?
The goal is always to maximize rig floor safety with experience based knowledge and innovative technologies. Obviously the experience is there after centuries of operations all around the globe but innovative technologies that are emerging must be incorporated sooner than later!
Current system of workplace safety has set of regulations and standards enforced by official organizations that apply to all rig floors around the world. OSHA and IADC have comprehensive guidelines some of which are just simple code of conducts to minimize human error.
Safe Footing and correct posture when lifting, pushing and pulling equipment can hugely impact rate of strains, slips, trips and falls.
Another major player is personal protective equipment (PPE) that covers head, eyes, hands, feet and fall protection. The materials and design are constantly innovated to improve visibility and protective features against temperature shock, humidity and impact. PPE should always be chosen based on most recent technology that offers actual protective results.
There are also simple rules of housekeeping so small equipments and objects do not remain on rig floor and cause trip and fall.
Supervised application of these safety measures is an integral part of the system so common tendencies of ignorance and neglect have no chance to cause accidents.
Then there are set of rules for the structure of rig floor so hazards are minimized. For example, rig flooring should be made from nonskid materials that are heavy duty and flat with high traction. They provide a safe base for footing when operation is underway and drilling fluid is splashed on the ground to prevent slip and fall. All machinery and equipment must be inspected and maintained on a regular basis so small machine errors do not lead to catastrophe.
There is also detection system which is focused on smoke, fire, gas and fluid leaks. It relies on detectors with sensors that are sensitive to certain chemicals.
The current system obviously has limitations because the technology is old and outdated in most cases. Detectors for example, are subject to environmental conditions that can hinder the accuracy of detection. That is why rogue readings by chemical sensors are very common. They respond to moisture in the air the same way they react to deadly gases! On the other hand, they can not identify all possible hazardous gases in the air! They can also get clogged by pollution and dirt which require regular cleaning and maintenance. Their range of detection might also be obstructed by objects such as trucks, columns or even birds!
On the other hand, real time safety monitoring relies only on supervisors who are subject to human error! Of course there are CCTV cameras but they are used solely for security purposes and real time monitoring of operation for safety purposes is missing in the chain!
That is where VEUNEX becomes relevant. A workplace safety system that imposes Ai models on live stream videos to identify, alert and prevent safety hazards in each scene.
It has pre-defined scenarios for all possible hazards which are learnt based on real data from past experiences. Images and videos are introduced to Ai so it can learn possible dangers. System settings for timing and contacts defines who gets the notification and when. It is designed to record safety anomalies, send notifications and alarm the site.
The scenarios cover all safety related rules that are supervised on site. All non-compliances with PPE, access limits and traffic safety are monitored. Upon detecting violation, notifications are sent out to relevant people. In case of fire and explosion, alarms go off on the site too and evacuation scenario is initiated immediately.
PPE scenario identifies lack of necessary PPE on personnel and notifies supervisors. High risk behaviors such as smoking, talking on mobile phone and standing close to edges when working from height are recognized. Detecting fallen person is easier with this Ai based system because it has learned to identify human posture in different situations. Wearable ID tags are also identified for immediate locating of staff which is helpful in case of emergencies.
The lifting scenario includes identifying standing people in crane fall zone or alerting unusual wind speed. If there are more people than required for each operation, a risk is detected.
Poor lighting and presence of visible safety signage are constantly checked. Poor housekeeping is also checked in real time so operations are managed without accidents caused by clutter on rig floor. And above all, cameras are evaluated constantly for proper function.
All detected risks are saved for later evaluation and further learning that can easily be managed through an intuitive interface. The HSE audit conducts risk analysis and takes into account all safety requirements based on recorded data and suggests adjustments to maximize rig floor safety.
The API can be integrated with other communication interfaces such as REST, PROFIBUS and MODBUS to cover both native and third party activities for extended efficiency in safety.
The system is scalable for future changes in rig floor structure. It is also customizable for individual requirements of each rig floor. With all these features, VEUNEX solution maximizes rig floor safety.
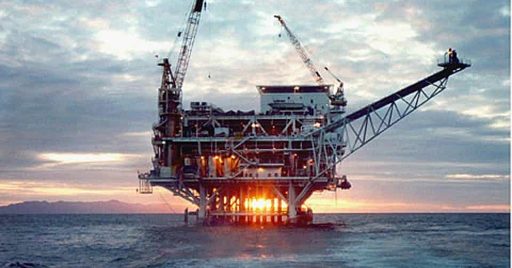
Conclusion
Rig floor safety has huge impact on the health of workers, ecosystem and investors. It shifts the numbers on financial statements in favor of costs while shifting the clock in favor of shorter life span.
Presence of heavy duty equipments and machinery, combustible gases and fluids and working from height increases the risk of being struck by objects, fire & explosion and slip & fall.
The only way to maximize rig floor safety is to upgrade safety technologies that are currently used on sites.
Ai based Intelligent HSE solution is the ultimate answer to rig floor safety. The fast evolving computer processing power with rapidly self learning artificial intelligence and machine vision can make magics in upstream safety. Ai powered rig floor safety is the dream come true of zero fatality and no loss for oil and gas industry.