Every year, common workplace health and safety hazards, including working at height, poor housekeeping, chemicals, ergonomics, and so on, cause many injuries and deaths.
Employers must be aware of all these occupational hazards, implement risk assessment, and strive to mitigate them as much as possible.
The seven typical workplace safety hazards lie as follows:
1- Ergonomic: common hazard between Office Job and Physical Job
Ergonomic hazards can harm workers’ musculoskeletal system. They are sometimes invisible, and usually, workers figure them out when the injuries get inevitable and cause pain.
The carpal tunnel is one of the most common musculoskeletal disorders among office workers who sit a long time at a computer.
Another widespread ergonomic hazard is back injuries. Not only office workers but also every other employee who moves or lifts heavy things are at the highest risks of back injuries.
According to the Bureau of Labor Statistics (BLS), in 2007, about 35 per 10,000 full-time workers in private industry required days away from work due to musculoskeletal disorders. Then employers must consider this hazard seriously to protect their staff and avoid loss.
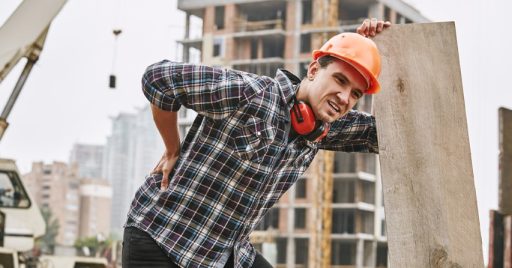
2- Housekeeping: It is not just about cleanness
A lot of occupational injuries are caused by poor housekeeping in the workplace. Although the most common poor housekeepings are slips, trips, and falls, this workplace hazard has been directly linked to many fatal accidents at work.
According to the Liberty Mutual Workplace Safety Index, in 2019, industries lost more than 17 billion dollars due to occupational injuries caused by slips, trips, and falls.
Slips, trips, and falls are not the only incidents that poor housekeeping could cause. In a warehouse, over-stacking loads on racks can disturb the sprinkler’s performance in a fire emergency, or leaving a barrel with inflammable liquid in a hot work area can cause horrible fire or explosion.
So employers must practice effective housekeeping to control and eliminate workplace hazards.
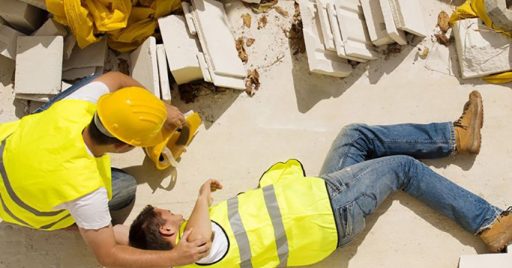
3- Confined spaces: The hazardous space in a workplace
There are several confined spaces in many workplaces, such as utility vaults, water supply towers, sewers, silos, vats, and hoppers. Working in a confined space could be more hazardous than an open workplace, and so many fatal incidents have occurred in those spaces.
Confined spaces contain health or safety hazards such as entrapment, engulfment, and hazardous atmospheric conditions. Then most of these spaces are permit required.
According to OSHA, all confined workspace that contains health or safety hazards must consider as a permit-required or restricted space.
Employers must implement a proper risk assessment over these dangerous areas and control entrance carefully.
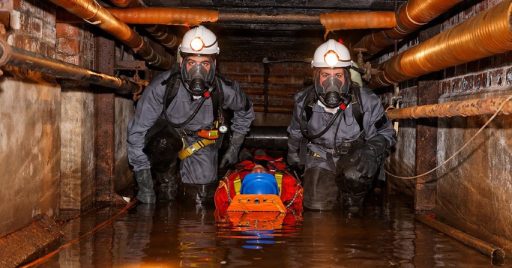
4- Working at height: The most dangerous activity in the construction industry
According to the Health & Safety Executive reports, in the UK, falls from height are the most dangerous activity with the highest fatal injuries. During 2019, around 30 people were killed due to falls from heights only in the united kingdom.
Among common construction hazards, work at heights accounts for more fatalities than any other activity.
Several factors like the vertical distance of fall, fragile roof, unstable or poorly maintained access equipment, and adverse weather conditions could cause falls. Steelworkers, welders, and painters are often the people who are exposed to risks from working at heights.
Employers must prevent working at heights as much as possible. Otherwise, they should plan the activity, consider proper work equipment, supervise it carefully by competent people, and consider emergency or rescue actions.
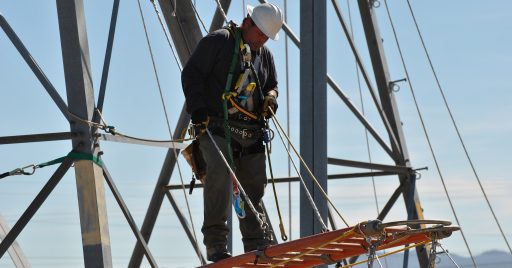
5- Chemicals: all of them can be dangerous, even water!
Working with toxic substances could be so dangerous, and people who work with hazardous chemicals must be aware of all hazards associated with each chemical and protective solutions.
Exposure to chemicals can cause not only deadly diseases but also some other accidents like a fire explosion. Some chemicals are flammable, some gas state chemicals are toxic for inhalation, and some other chemicals are dangerous to be touched.
Employers must hire professional workers and teach them all hazardous chemical features. They have to implement risk assessment and provide essential PPE to protect employees from exposure to dangerous chemicals.

6- Electrical: don't get shocked!
According to the electrical safety foundation international (ESFI), from 2003 to 2018, 3% of all workplace fatalities were caused by contact/exposure to electricity.
Electrical hazards can cause electrocution, shock, burn, fire, explosion, and some indirect injuries like cuts, broken bones, and falls.
OSHA has required that all the employers provide essential personal protective equipment (PPE) to protect workers exposed to eye or face hazards and consider proper Lockout/Tagout practices and procedures to safeguard workers from the release of hazardous energy.
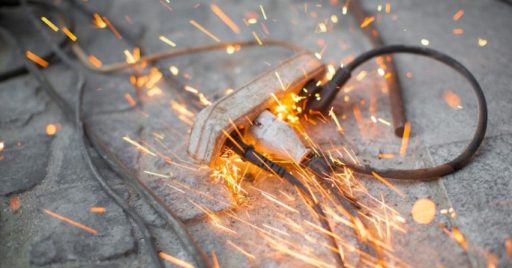
7- Forklifts:
In 2018, according to injury facts, forklifts accidents caused 85 death and 7,940 injuries.
Forklift operators often are the main responsible person in all those accidents. In one fatal case investigated by OSHA, since the loaded boxes obstructed the operator view, the forklift hit a worker and killed him. In another case, in 2019, a forklift overturned and caused one employee’s death.
Forklift operators must be well trained and aware of all possible accidents.
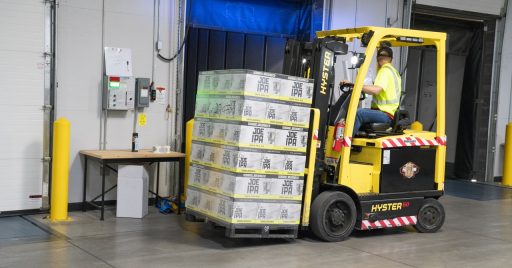
Employers must consider all mentioned hazards in the workplace health and safety plan. According to the international labor organization, over 6000 workers succumb to death every day due to workplace-related accidents or diseases.
Employers must find new solutions to protect workers from occupational hazards, and now through artificial intelligence, Veunex puts new ideas on the table!