Using AI for refinery maintenance is a smart choice because it can help with both planning the overhaul and during maintenance in oil refinery.
Machine learning can be used for predictive maintenance because the past data gathered from refinery industry can help predict the useful lifespan of equipments so replacements are installed on time.
AI can also be used for preventive maintenance to schedule the best refinery overhaul intervals for optimum functionality of equipments based on the predicted lifespan. This way corrosion and deposit formations are identified on time and equipment integrity is maintained at its best.
AI can also be utilized for corrective maintenance since machine failures can be predicted.
However, during refinery maintenance, AI is able to supervise the whole process in real time and send out notifications to managers and HSE professionals, so they can take immediate action and prevent accidents.
This is extremely critical because AI can overcome the limitations of current safety systems and reduce accidents during overhaul in oil refinery. Currently the rate of incidents are high in refinery maintenance but the exact numbers are not recorded by officials because majority of work is done by outsourced contractors.
One such incident occurred at Sannazzaro de’ Burgondi refinery near Milan on December 1st, 2016 that was 24 days into a 30-day scheduled turnaround. Fortunately there was no fatalities but a massive blast erupted that send flames and black smoke into the air.
In this article, we will highlight 7 ways AI can reduce accidents during maintenance in oil refinery so managers can make informed decisions about their intelligent HSE systems.
Table of content
7 ways AI can reduce accidents during maintenance in oil refinery
One of the greatest advantages of machine learning is its detecting capability that is learnt from massive data collected from the oil and gas industry. AI, being a machine is immune to human error so it doesn’t fall into the trap of emotions, boredom or ignorance. Instead, it does the detecting job without interruption. This ability makes AI a perfect real time supervisor that is present in all locations at once during overhaul to detect the following safety violations:
1. Supervising PPE violations
PPE are the most critical safety equipments that exists for workers during overhaul in oil refinery due to the fact that up to 30,000 procedures are performed that cause massive amount of chemical and mechanical hazards.
There is also the number of workers that multiplies in this period to engage in non-standard activities such as draining and flushing with long shifts and excessive overtime all of which just amplify the possibility of accidents!
Refinery maintenance and overhaul also utilizes massive amounts of hazardous chemicals such as arsenic, benzene, HCI acids and hydrogen sulfide that require specialty PPE to protect the face and respiratory system more than usual.
Modern PPE can provide workers with fall protection by safety vest and harness, flame resistant gear & rain suit, hard hat for falling objects, clear face shield, helmet and respirator masks for chemical and particulate exposure, industrial ear plugs for hearing loss prevention, impact resistant goggles for full eye protection, cut resistant gloves for all the abrasive handling and steel-toed boots for feet protection against falling objects and slippery floors.
AI and machine learning can identify the correct PPE for every operation and sound the alarm if it is not used by the worker. It can even recognize absent of fire extinguisher or HSE staff! Considering the system is available behind every CCTV camera, the rate of reduction in accidents during maintenance in oil refinery will be high which is the most cost effective strategy.
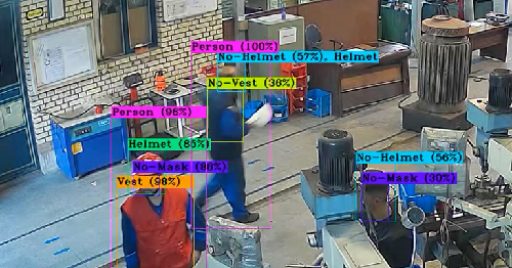
2. Detecting poor ergonomics
Many of ergonomic injuries such as strains, spasms, cuts and burns that are resulted from trips, falls, being struck by or caught between objects during refinery maintenance can be prevented if workers commit to holding safe footing & posture.
Getting in and out of confined spaces such as tanks during refinery maintenance cleaning, standing at the edge of elevated levels when replacing equipment parts, standing under flying tubulars that are being installed, putting all the pressure on lower back when bending, pulling or pushing objects are all risky behaviors that can be detected and notified by AI-based HSE system. The best part of this process is that workers learn to uphold such footing & posture after repeated alerts!
3. Detecting fallen person
Machine learning is capable of recognizing when a human is fallen on the ground since it has learnt human posture in different situations through training data. This is most helpful in case of sudden accidents or health crisis during refinery maintenance and overhaul such as shortness of breath due to chemical exposure or heart attack and epileptic seizures in which AI can notify medical team as soon as incident happens.
It is also capable of face recognition to identify the worker in a falling accident. Even wearable ID can be identified easily for emergency cases. The extent of help is vast since much more data such as blood type or special needs can be associated with the ID for life saving medical emergencies.
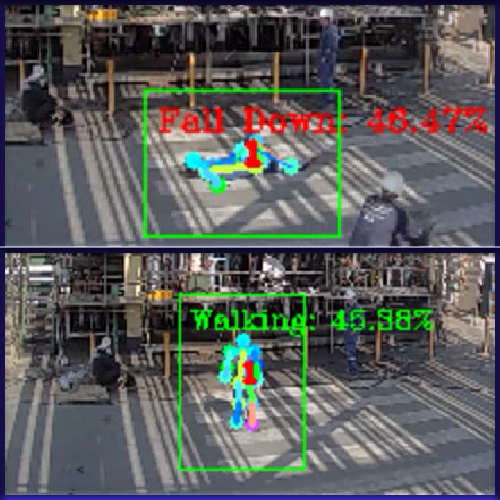
4. Detecting dangerous behaviors
AI is capable of identifying risky behaviors such as access limit violations, excessive number of people on board, working in low light, smoking, using mobile phone and poor house keeping all of which are causes of injuries and fire incidents.
It can also identify cars by their plate who have unauthorized entry or violate driving speed limits which is a major cause of incidents around refineries.
Considering the number of workers multiply during refinery maintenance, the number of risky behaviors might increase as well but AI can reduce accidents by catching them in real time!
5. Detecting leaks
Leaks are the most common sources of hazard during refinery maintenance since tanks are being blasted and pipes are being drained. The cleaning equipments are full of chemicals and fuels that can also leak. There is large amount of waste water too that can be contaminated. Detected on time by AI, it is possible to prevent a leak from turning into a disaster.
6. Detecting smoke & fire
With presence of massive heat generating operations such as welding during refinery maintenance, the possibility of fire hazard is really high. But small fire detected on time can be extinguished to prevent catastrophic accidents. That is where AI is most useful because it has learnt to detect even the smallest smokes and fires, sound the alarms immediately and initiate extinguishing process.
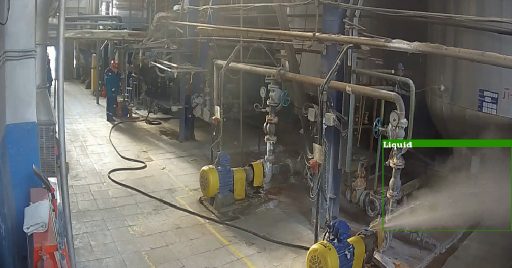
7. Detecting weather changes
Although oil refineries are armed with good weather prediction system but adding machine learning to the mix can enhance the process. Predicting the optimal time to start refinery maintenance and overhaul is the key to its success. But in case of unexpected shutdowns, AI can predict the exact time and level of damage based on past experiences and suggest the best course of action to reduce accidents.
Conclusion
AI can reduce accidents during refinery maintenance and overhaul by supervising the operation in real time and detecting human errors such as PPE violations, poor ergonomics and dangerous behaviors as well as machine errors and early leaks, smoke and fire.
AI and machine learning are disrupting oil and gas industry for enhanced safety so workers, environment and investments are all protected. They are bringing Oil and Gas 4.0 to the entire industry so sustainable safety becomes the new norm.
By implementing machine learning in oil refinery, huge amount of operational cost can be saved on unnecessary downtimes and accidents during overhaul so the oil market can thrive again post COVID pandemic.
A data driven refinery is a safe work place for the whole ecosystem and that is why the big players such as BP ad Shell have already joined the game by using AI-based HSE solutions.