The steel industry is the heart of global economic development, with over 6 million workers and 2.5 trillion dollars sold products every year. Therefore occupational health and safety in such a vast industry are so vital.
According to the Bureau of Labor Statistics, from 2015 till 2018, fatal accidents in the US steel industry caused 68 deaths, and a statistical review of occupational injuries shows that in 2007, over 155 thousand fatal and non-fatal accidents occurred in the metal industry in Europe.
All mentioned numbers confirm how much occupational health and safety is essential in the iron and steel industry. Employers and safety managers must recognize iron and steel industry hazards and implement specific measures to prevent accidents.
This article is based on the ILO revised code of practice on safety and health in the iron and steel industry and tries to summarize safety hazards in the steel industry.
Table of content
Confined space
Confined spaces are large enough to enter and work in, but their entrance or exit are restricted, and work in such places must not take a long time or be continuous.
Employers must follow the OSH advice or a similar authority regarding compliance with national legislation and regulation. They must identify and inspect the workplace’s confined spaces to recognize all related hazards like flammable vapors and gases, electrical and mechanical.
Employees and contractor workers must be trained about working in confined spaces and informed of hazards, protective measures, and emergency rescue procedures.
Hazards must be eliminated or controlled as much as possible. On the other hand, to ensure the worker’s adequate protection, employers must provide essential personal protective equipment, including rescue devices.
Suppose a confined space remains still dangerous, and hazard elimination is not efficiently possible. In that case, it must be clearly marked with warning signs and entry must be restricted by authorized permission.
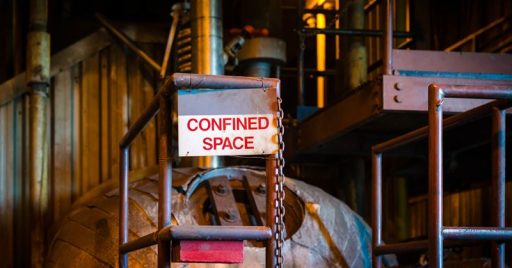
Hazardous energy
Different energy sources like electric, mechanical, hydraulic, and pneumatic are regularly used in the steel industry. The source of energy should be isolated rather than the control mechanism; otherwise, employers must consider a safe procedure to control them in the health and safety management system. It must include preparation for a shutdown since many accidents occur during a shutdown.
Besides, workers who carry out the procedure must be appropriately trained in accordance with the nature of the energy source and the characteristics of the facilities; a tag-out application must be applied, and everyone working on equipment or systems should be informed of it.
Work equipment and machinery
Working with machinery and even hand and portable power tools may result in accidents, many of which are severe and some fatal. Therefore employers must implement risk assessment and be aware of all work equipment and machinery hazards.
Many accidents happen when the wrong equipment is used for work, so operations must be planned ahead. On the other hand, employers must consider using safe guards where ever machinery has hazards to eliminate possible dangers as much as possible.
Every piece of equipment and machinery must be regularly checked and maintained. Even a broken hammer can cause injuries.
Cranes and hoists
All machinery used to lift or transport equipment, materials, goods, etc., must be installed, operated, and maintained as specified by the manufacturer. Their operators must be well trained and professional.
Employers must consider a safety procedure for using cranes and hoists. A safety crew member must monitor the lifting operation, and the safety distance between the crane and workers must be carefully considered. Transport routes for cranes should be clear of obstructions, and in the case of molten metal, free of water.
The lifting load must not exceed the capacity, and the hoists’ structure must be well designed to bear the burden. The lifting or lowering must be implemented slowly and smoothly.
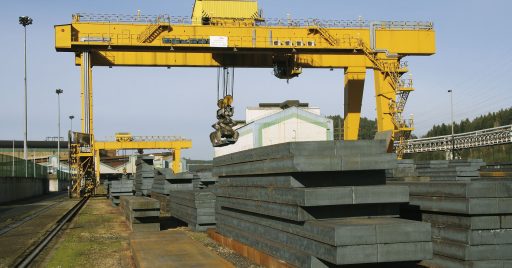
Falling objects
Falling materials can cause fatal accidents or severe injuries. Therefore, employers must consider the risk to protect people in the workplace, and all essential measures must be regarded as to prevent falling materials or objects.
The area must be clean, and the walkways must be covered with alternative safeguards such as safety nets. Employers must provide mandatory PPE such as hard hats besides install danger signboards to warn workers.
Slips, trips, and falls
Slips, trips and falls are not dangerous only in the oil and steel industry. They are among the typical hazards in all workplaces and must be considered in the occupational health and safety management system.
The floor must be clean and regularly kept clean of oil or water to be prevented from slips. All obstacles on the floor must be well-considered and managed. Tools, materials, and equipment must be in specific locations.
Steel floor plates should be made slip-resistant and non-combustible. Floor openings should be covered with clear warning signs, and all working areas should always be well lit.