Digital transformation in downstream oil and gas industry is a given. It is how plants should be designed. Everything is becoming digital for the good of all, the workers, the environment and the investments.
In this article, we will look at how digital transformation is affecting the downstream oil and gas industry by reviewing trends, key benefits and barriers. So managers have a clear mind for the decisions they have to make for digitalization of their companies.
Table of content
Key Trends of digital transformation in downstream
The digital transformation in downstream industry is in early stages. Meaning, the field is wide open for managers to take a data-driven approach for digitalizing their organization.
The ease of digitalization really depends on the age of the asset. Greenfield plants are most likely the most digitalized because it is easier for a new asset to be digitalized from the beginning. But brownfield plants are the most challenging.
The retail side of downstream is also highly digitalized duo to direct interaction with customers but inside refineries, legacy systems are still the main mechanism.
Some organizations such as EPC Europe however have completed the phase one of digitalization initiative so even all equipments in the plant are scanned and assigned attributes!
According to this report, there is great growth in capacity within the Middle East refining sector due to the need to diversify economies from heavily reliant on crude export revenues to refinery products. This creates a tougher competition for ageing facilities in Western Europe to optimize their assets by digitalization. The new and complex facilities in APAC that are able to process lower quality and cheaper feedstock, just accelerate this digitalization process.
In gas processing however, the high demand from global push to use cleaner fuels drives the supply which shifts the operators towards natural gas production from 90% oil to 70% gas. Regardless of upgrading existing assets or building new facilities, digitalization and intelligent data management are the promising mechanisms for optimized productivity and profitability. This approach allows progressive operators to turn digital transformation in downstream to a competitive advantage.
Digital transformation in downstream through AI technology is even used to predict consumer demand for petroleum products as well as measuring supply shortages and recommendation for a mix of oil for a refining process.
But a major trend is AI-based HSE systems that are taking the industry by storm. The supervision in real time, will maximize workplace safety which leads to a much lower claimed injuries and environmental damages. Ai and machine learning are capable of learning to detect safety hazards and violations such as PPE use or early fire and notify HSE managers to take immediate action.
Key Benefits of digital transformation in downstream
Benefits of digital transformation in downstream are enormous but can be summarized in following categories:
• Greater efficiency
When it comes to assets, maintenance is the key driver since unplanned downtime will hugely affect revenues.
That is why a proactive maintenance approach is essential which starts with planning. But the plan itself is affected by short term and long term market drivers. The pressure of demand and supply in the long term and feedstock pricing in the short term both also affected by economy and regulations can dramatically change a maintenance plan if they are not already considered.
Digital transformation in downstream by automation solutions will make prediction and prevention easier in turnaround planning so asset uptime is enhanced and downtimes are reduced.
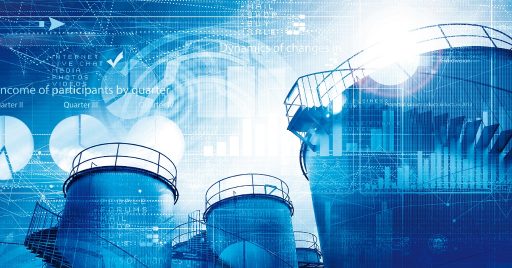
• Better asset utilization
Your employees, customers and business partners are at the center of digitalization since they directly interact with the system.
They need to understand the change, the process and functionality of the new data driven system. They need to be trained on collecting and interpreting data so they can have the right input and output.
There might be some cultural barriers such as resistance to change that can be overcome with enhancing adaptive skills and filling the skill gaps. Open-source learning has proven effective in re-skilling employees in a short time.
• Decreased costs
OPEX makes up majority of downstream costs. With lower maintenance costs which is essential for higher asset utilization, the OPEX will shift dramatically. Elimination of shutdowns alone can remove the adverse effect it has on financial health of the downstream.
The maintenance cost in both gas processing and refinery segments are dominated by asset services with 72% share which deals with structural, electrical and mechanical systems while the asset integrity including support for asset services efficiency makes up the rest of maintenance works. Both categories can be enhanced with data driven solutions and machine learning.
There is also the reduced cost of human resources as fewer personnel are required for operations.
Above all, there is the cost of injuries and fatalities as well as damage to the environment that will be reduced greatly by using artificial intelligence to supervise operations and detect safety hazards and violations.
• Increased profitability
Asset utilization is a major driver when it comes to profitability which is mostly affected by unplanned maintenance.
Ensuring asset safety and optimizing asset uptime within a digitalized maintenance plan will ensure the revenue currents keep flowing without interruption.
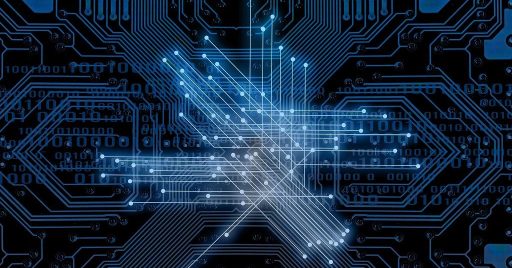
Key Barriers in digital transformation in downstream
To reap the benefits, barriers must be overcome which starts with ensuring accuracy of data. Flow of data must be comprehensive and data communication must be trained so every one understands how to use and interpret the data.
The legacy systems in brownfield plants are another major challenge since they require major upgrades in sensor and detecting systems for a better predictive and prescriptive maintenance.
Conclusion
Digital transformation in downstream oil and gas is the core focus of the industry and like any other innovation, it has benefits as well as barriers.
By taking a data driven approach, the asset utilization will be enhanced resulting in higher efficiency and profits. The maintenance cost which is a key driver, will be lowered by proper planning so unplanned downtimes are eliminated. But it all depends on the accuracy of data collected and proper training of those involved with the data. Legacy systems present in brownfield plants also pose a major challenge.
But progressive companies of both petrochemicals and refining have already chosen digital transformation at all stages from design and planning to predicting customer demands and HSE.
Digital transformation by AI is the most advanced competitive edge a downstream company can have and intelligent HSE solutions are a big part of it.