Digital Transformation of Drilling Rigs is coming and the magical results will change the future for the good of all.
Artificial intelligence (AI), machine learning (ML) and Industrial Internet of Things (IIoT) are revolutionizing the upstream oil and gas industry with rapid pace and the outcomes benefit everyone, from workers to planet and investors. They are the solution everyone was waiting for!
In this article, we will explore how Digital Transformation of Drilling Rigs will change the future to help managers make the most of evolving technologies.
Table of content
8 major changes by Digital Transformation of Drilling Rigs
Change is good specifically for the old oil and gas industry that has experienced many safety incidents in its long history and has struggled with increasing costs and low prices. The most recent being the negative price at the beginning of COVID pandemic!
The changes by Digital Transformation of Drilling Rigs cover all aspects of upstream business but can be categorized in the following 8 major changes:
1. Effective rig design
Rig design has always relied on belt and suspender redundancies to make sure accidents won’t happen. Digitalization by artificial intelligence will eliminate this need because the study of historical data will reveal the actual shortcomings. The new solution will eliminate the fault leading to huge amount of capital costs for drilling equipments and services to be freed.
2. Improved manufacturing process
With automation, delivery of drilling tools, services and parts will be on time. Therefore, offshore drilling logistics will improve and operations will be performed as scheduled. This streamlining of manufacturing process will save time and budget from being wasted.
3. Quick product development
AI and ML will revolutionize product development due to the shorter time frame from few months to days. Data analytics of product design and test has a huge role as it compares past products that had similar functions. This intelligent process will recognize the features that historically contributed to failures.
Digital Transformation of Drilling Rigs by artificial intelligence and machine learning will provide new solutions for old problems such as machinery that have low cycle counts and expensive maintenance cost with the need to redundant systems. The new solutions will significantly reduce OPEX and CAPEX.
4. Additive manufacturing (AM)
3D printing as it is also called can manufacture parts made from both the polymers and metals which have more complex geometries and smaller sizes. This can have capital saving effect on spare part inventory and heavy assets. Local printers can lower the frequency of transporting parts by air or truck which is highly cost effective.
Transportation of drilling tools to the rig site will also change dramatically as AM takes place of current conventional methods. AM equipments can be attached to drill string for printing purposes of casing, tubing, hangers and liners while string is inside the hole. Not only time will be saved but transportation costs will reduce significantly.
5. Condition-based maintenance (CBM)
Powered by the network of sensors and devices that make the Industrial Internet of Things (IIoT), CBM will eliminate failures and extend life span of equipment. Machine malfunction will become a thing of the past that caused many fatal accidents.
It will change the CAPEX structure of the entire rig including size of both the rig and parts inventory leading to a more streamlined supply chain and a lower development cost.
It also helps with asset management based on priority that allocates crew to a site with urgent need to attention and limits the windshield time resulting in a lower-cost rig management.
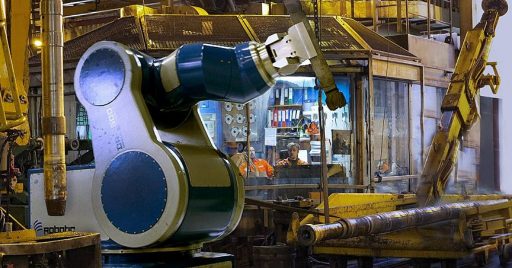
6. Eliminated repetitive operations
The boring operations that has always bothered humans will be performed by robotics more safely because they don’t get tired or distracted so mistakes are eliminated. They can also perform multiple tasks by just changing the appendage at the end of the arm. Digital Transformation of Drilling Rigs by robotics will result in altered maintenance routine and lower training costs while workers can engage in more creative and exciting tasks.
7. Eliminated drill pipe incidents
Rig automation will increase efficiency and safety leading to elimination of pipe string getting stuck. Supply chain and logistics will benefit the most with fewer number of drill pipe incidents that often drive higher spending.
From the delivery by truck to pipe rack, ramp and rotary table, the whole chain of actions will be efficient and human-free which protects workers from being struck by drill pipes or getting caught between them and their hand will definitely be saved from contact with heavy metal.
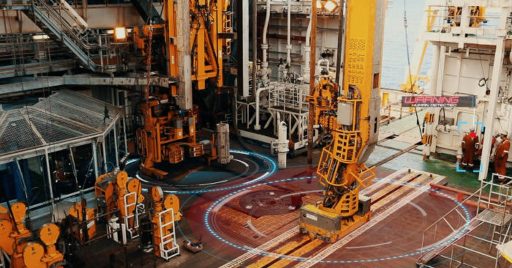
8. High Intelligent HSE
AI is powering work place safety by learning from past data and detecting similar scenarios in real time. Remote supervision is the new normal to make sure all drilling rig safety protocols are applied and HSE metrics are in a healthy range. Remote configuration of drilling operations by process supervisors who will replace floor hands leads to efficient HSE.
Machine learning coupled with CCTV cameras notifies HSE managers about safety hazards and violations at all places at once. This will prevent PPE violations, ergonomic mistakes, dangerous behaviors, entry to red zones, leaks and fire & explosion. The result is a work place free from high rate of human error that leads to lower injuries and fatalities which have always drive costs.
Conclusion
Digital Transformation of Drilling Rigs will change the future by freeing humans from boring repeated works and dangerous operations. It is eliminating drilling pipe incidents which are the main hazards in oil rigs. Maintenance process is becoming more effective resulting in longer life span of equipments and safety. The design of both the rig and equipments are improving for better functionality. All this productive changes result in lower capital and operating expenses of drilling operations and rig management which are central to the choices a manager should make.
But a more important Digital Transformation of Drilling Rigs is happening in HSE which is utilizing artificial intelligence for real time monitoring of safety hazards and violations. The AI-based HSE will save lives and environment beyond imagination.