Drilling operations are considered high risk from every standpoint because rig safety depends on many important factors, some of which are out of control. Unexpected challenges such as harsh weather conditions are always possible specifically on offshore rigs but precautions should be taken for such cases in safety management of drilling operations.
There is also human error which plays a key role in drilling rig safety but organizational policies are also involved. The data from IADC reveals 266 drilling rig incidents have occured in 2021 (till the end of second quarter) as result of these factors.
In this article, we will explore safety in drilling operations and list the most common risks and necessary precautions to help HSE students and professionals gain a broader knowledge of their tasks.
Table of content
What safety risks are involved in drilling operations?
Drilling rig is a massive construction built in remote locations that has numerous parts including derrick, rig floor, doghouse, cellar, the pit and pipe racks. The location and parts impose their own hazards in drilling operations which can be summarized in following risks:
• Harsh weather conditions
Depending on the location and layout of the rig, natural hazards are frequently experienced. Offshore, it can be storms and tides with humidity and sun exposure but onshore it is extreme temperatures of either heat or cold. They all can lead to malfunction of equipment or collapse of structure.
These location based risks can also influence mental and emotional health of workers that coupled with isolation, long shifts, humid working environment, excessive noises and heavy equipments might result in poor attention and terrible accidents.
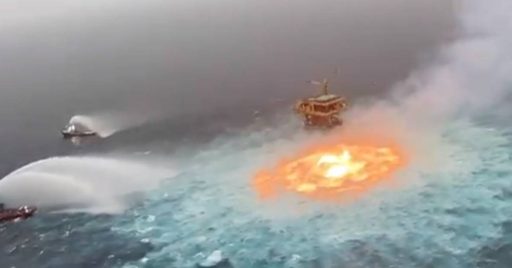
• Fire and explosion
With presence of massive amount of oil and gas in upstream industry, possibility of fire and explosion is really high. A small electronic spark or leak of an odorless gas might lead to disasters.
• Chemical toxicity
Oil and gas alone are toxic enough for human inhalation or skin contact but there are underground formations that contain hydrogen sulfide and have risk of over pressurization. The drilling fluid or mud is also toxic for humans.
• Machine malfunction
Machines can work for a certain life span if they are maintained properly. Otherwise they might malfunction when least expected and result in catastrophic accidents.
Each part of drilling operation might break or they might not be secured correctly. For example if Kelly hose is not secured with chains, it might snap and injure workers. If V-Door opening is not guarded, it might let the drill pipes slide down the ramp and hit someone.
• Heavy equipment strike
From drill pipes to cranes and rotating drill string or tongs, all equipments of drilling operation are heavy duty irons that can strike a worker out of nowhere and cause severe injuries. The risks are even higher at some operations such as tripping in/out or casing.
• Slip and fall
The slippery rig floor is a breeding ground for slip and falls but elevated working spaces which are common on rigs are major causes of falling accidents.
There are also floor holes on rig floor or the crown that might just pull in a worker. The open pits for excess water and drilling fluid might also become a site for trips and falls.
What precautions should be taken to prevent accidents in drilling operations?
Each identified risk must have safety precautions during drilling operations that can be summarized in following actions:
• Emergency response plans
Being prepared is the key to overcoming emergencies such as blowout of crude oil. It starts with training of all staff. Availability of adequate rescue equipments is also crucial. The purpose is to save life, stabilize incidents and conserve property.
• Detection sensors
To prevent fire and explosion, it is absolutely essential to detect smoke, gas leak and small fires. The high tech sensors should be able to identify all possible hazards in drilling operations.
• Safety lighting and visible signage
Lighting plays a key role for safety in drilling operations due to the complexity of the structure that might need more light for visibility. Presence of open pits also necessities more lighting.
Safety signages are also required throughout drilling rig to remind workers of dangerous behaviors and access limits.
• Machinery maintenance and protection
Maintenance, repair and overhaul (MRO) must be scheduled rigorously to make sure functionality of machines are intact.
Guards and rails are necessary to lock each part of drilling equipments in place. Electrical surge protection is also necessary to prevent sparks and explosions or power outage.
Safety Tool Boxes are also essential for lockout/tagout procedures and proper handling of energized or mechanical equipments.
• Regular safety training
The staff training must cover every aspect of safety in drilling operation from evacuation procedure at the time of crisis to handling of equipments and materials along with holding proper posture and footing specifically at height or on slippery surfaces.
Even helicopter crash survival and firefighting should be included. But above all they must learn to follow instructions and protocols instead of self regulating safety risks!
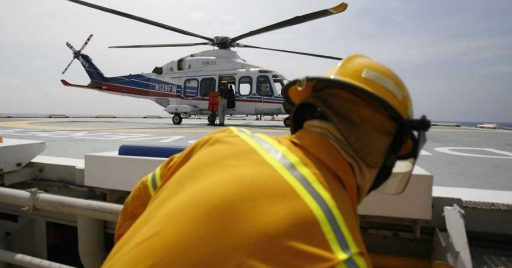
• Non-stop supervision
Drilling operation can be dangerous and human error has a part in it. So on-site supervision is always a necessity to add an extra layer of safety.
• Adequate PPE in good condition
Personal protective equipments or PPE are essential part of safety in drilling operations. Geronimo line for monkey board, heavy duty boots for slippery ground, hard hat, gloves and goggles are required at all times but waterproof garments, flame resistant clothing, hearing and respiratory protection are also necessary. wearable ID tags are very helpful at the time of crisis to quickly locate workers anywhere on site.
• House keeping common sense
Common sense is a good skill when it comes to house keeping so small objects don’t lead to fatal falling accidents.
Conclusion
Safety in drilling operations is critical to prevent small problems turn into catastrophic events. The risks such as fire and explosion or falling are high as are equipment and material handling. That is why precautions such as regular training, equipment maintenance, availability of safety tool boxes and PPE are absolutely essential to properly handle the risks. They all must be considered in details in risk assessment and safety plan.
What can be more effective is an Intelligent HSE system that supervises process safety in drilling operations in real time through CCTV cameras and sends out precautionary notifications for every identified risk.