Overhaul/Maintenance operation in oil refinery is a critical component of MRO process which stands for maintenance, repair and overhaul. It insures the oil refinery can operate safely during its lifespan and maybe beyond. But like any major project that involves explosive fuels, heavy equipments and also human errors, it might create safety issues that must be handled within an Intelligent HSE system.
In this article, we will explore the safety issues that might arise during overhaul/maintenance operation in oil refinery so HSE professionals and managers are aware of the possible risks and take precautions and safety measures.
Table of content
What is overhaul/maintenance operation in oil refinery?
According to Energy Assurance Daily of US Department of Energy, there were more than 1700 refinery shutdowns just in 2009-2012 in which 46% were caused by mechanical issues, 23% by maintenance, 19% by power failure and 12% by other accidents.
This figures are only a glimpse of what might happen in an oil refinery due to accidents and failures. That is why overhaul/maintenance operations are pre-planned so no unexpected shutdown occurs due to equipment failure and no safety issue arises during overhaul/maintenance operation in oil refinery.
Overhaul/Maintenance operations involve routine inspections for corrosion & deposit formations and integrity of equipments. There are also special inspections for anomalies in major equipments along with replacements & installments of equipments and process materials.
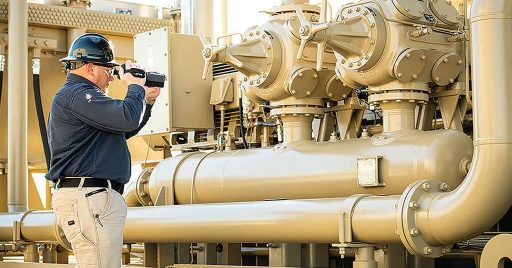
Maintenance operations might be done while oil refinery is in operation in which case they are often minor fixes. Or they might be forced by an unexpected shutdown resulted from natural disasters. But mostly, they might be performed during a planned shutdown which is called turnaround.
A turnaround might take 1-2 years of advanced planning and be completed in several weeks or months depending on the extent of inspection and the problems that are found. It is often scheduled for a time when production is at its lowest and materials and skilled labour are available. It is a very expensive project because it requires thousands of outside contractors and losing of income for a long shutdown. However, it might be required every 3 to 5 years!
It might be a preventive process to prevent unscheduled shutdowns that is performed in scheduled intervals based on the age and remaining lifespan of an equipment. It can include cleaning, flushing, changing oil, tightening bolts and lubricating equipments.
Or it might be a predictive process to predict damage and failures before they occur. It uses measurements and signal processing in addition to oil and gas engineering to estimate the useful lifespan of an equipment. That is why it is also called condition-based monitoring.
Or it might be corrective process to restore a failing equipment back to its operating conditions by welding, adjusting fixtures or sealing.
Overhaul/maintenance operations are also an integral part of an asset integrity management (AIM) program that dedicate time to develop and implement strategies that optimize production with cost-effective maintenance techniques.
What safety issues are involved with overhaul/maintenance operation in oil refinery?
The whole process of overhaul/maintenance might cause safety issues due to presence of chemical and mechanical hazards but the most dangerous time is at the end of a turnaround when units are being brought back online.
In 2005 there was an accident at the end of a 9-week turnaround operation that killed 15 and injured more than 180 workers at a Texas City refinery. It occurred when the isomerization unit was restarted after being offline for two weeks.
Fortunately, these fatal accidents are rare but safety issues are common in current safety systems which include the followings:
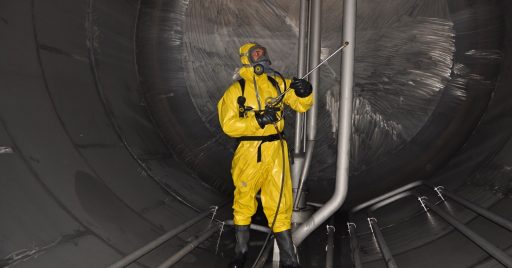
• Chemical exposure
Majority of overhaul/maintenance operations incorporate some sort of chemicals be it acids, additives, corrosives, solvents and wastewater. Some operations such as hydroblasting involves arsenic and hydrogen sulfide which are toxic. There are also citric and HCI acids, ammonia, benzene and hydrogen fluoride that might be used in different operations such as pipe draining repairs, tank cleaning, catalyst removal and insulation removal, all of which are hazardous to humans.
• Particulate exposure
Dust and particulates are created in many maintenance operations in oil refineries such as abrasive blasting that can seriously damage human skin, eyes and lungs.
• Excessive noise exposure
There are many overhaul/maintenance operation in oil refinery such as hydroblasting and flushing that generate noise beyond normal that also need noisy generators for electrical power! This level of noises are harmful for human ears that has long term effects.
• Abrasive and sharp surfaces
Many abrasive and sharp objects and vessels are being moved within the site that might cause cuts and lacerations.
Welding and cutting operations also create abrasive and sharp surfaces that are hazardous to human skin.
Tubulars are also prone to corrosion that creates abrasive surface for human hand during handling.
• Struck-by or caught-between objects
Almost 59% of workplace safety incidents in oil refinery is attributed to being struck by or caught between objects.
Tubulars have the highest rate by 12% which are replaced during maintenance operation in oil refinery. But heavy duty hoses and chains also contribute to the problem not to mention that almost all equipments are made from heavy iron that might be flying over head or falling from height and result in serious injuries.
• Fall & slip
Elevated work stations, slippery surfaces and possible poor house keeping can easily cause trips, slips and falls. Climbing stairs, ladders and elevators or standing too close to edges in addition to presence of tubulars, open pits and floor holes in poor lighting condition can all contribute to falling incidents resulting in long term damage.
• Fire & explosion
Presence of massive amount of oil in addition to hot works such as welding can turn an oil refinery into a perfect site for fire and explosions. Harsh weather conditions such as thunderstorms in addition to static electricity can also initiate a fire which has devastating consequences for ecosystem.
Conclusion
Overhaul/Maintenance operation in oil refinery is essential for work place safety because it keeps the whole infrastructure in safe working condition. But the process itself might become a source of safety issues if process safety management is not planned and executed.
An HSE solution that is powered by artificial intelligence can be incorporated for real time supervision of maintenance operation in oil refinery so workers, environment and assets remain perfectly safe.